Robots are growing and impacting the way society, economy and the world are organized. Areas with the lowest income, usually rural regions, are more vulnerable to the progress of automation. The permanent loss of jobs will be softened by new jobs that’ll be created and demand new skills from people.
Automation is likely to increase economic growth and boost productivity but it’ll also increase inequality among the globe and drastically change it. When should we start preparing for these changes? Now. And how? Let’s that a look at Oxford Economic’s latest report and find out.
What’s This Automation All About And Where Does It Come From?
The robotics industry is growing. And it’s growing fast. In 2016, the automotive industry accounted for a quite significant 43% of the total operational stock of industrial robots in global manufacturing. If you’re not getting the full picture, try it this way: imagine machines, probably with a whitish-grey look. Automatically controlled and reprogrammable. If they are young enough (recent ones) they’re probably powered with AI or even with machine learning – and likely responsive to their surroundings.
Their hobbies go from processing materials (such as mechanical grinding), (dis)assembling, painting, precision welding, inspecting or packaging. And as technology develops, they get more in shape as their energy storage improves. They don’t seem to complain and they’re getting keen on interacting and collaborating with humans – and optimizing productivity, especially and mostly (at least for now) in the manufacturing and logistics areas.
Just a quick throwback to the numbers – since 2010, the industrial global stock of robots grew in more than half. Or, in different words, during the last 4 years, the same number of robots were installed than in the previous 8 years. And where are they coming from and going to – you wisely ask. And perhaps not surprisingly, around 1 in every 3 robots worldwide are now installed in China. In fact, the Chinese account for one-fifth of the world’s total stock of robots and accounts for ~35% of their global sales too. Korea, Taiwan, or India are some other big manufacturers.
- Related:
3 Reasons Why Automation Is Coming (Hard)
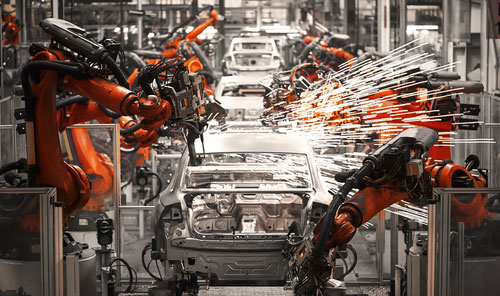
The study from Oxford Economics identified 3 main reasons why robot adoption is coming at an increasingly faster pace: price, innovation application, and demand. Number 1, price, has to do with the fact that humans are now more expensive than robots. Simply put, the smarter networks, the growth in the processing power of microchips or the extended battery lives made the average unit price of a robot fall down by 11% between 2011 and 2016. And the rise of the unit labor costs in manufacturing of China by over 65% since 2008 is also pushing for robots as the cheapest alternative.
Furthermore, as technology develops, processes get more sophisticated, robots become smaller, more sensitive to their surroundings and more cooperative with humans. Moreover, machine learning and the ability to learn from a huge and continuous amount of data, coming from a connected network of different robots, at an incredible speed is making robots more capable. More powerful. More desirable.
Regarding demand, China is expected to have nearly 8 million industrial robots in use by 2030. The Chinese are already and will continue global manufacturing leaders in items such as batteries, semiconductors, and other consumer electronic devices. They’re positively responding to the rising demand for manufactured goods and positioning themselves right in the heart of these changes for the long term.
Robots Are Coming – The Consequences And Impacts Of Automation
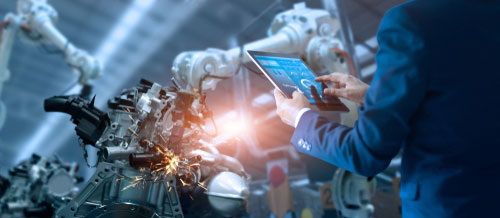
Right here, right now, things are nothing like they used to be. And they’ll surely look different too in the coming years. If we look back, since the year 2000, 1.7 million manufacturing jobs became extinct. If we look forward, at the current pace robots and automation are developing, 20 million manufacturing jobs might disappear globally. So yes, there’s a clear negative correlation between the rise of the robots species and the decline of manufacturing jobs performed by the homo sapiens sapiens.
But how is this employment impact distributed? – You’re probably wisely wondering again. Well, the fact is that jobs are affected differently according to their geography. For instance, installing one extra industrial robot in a lower income-region leads to 2x as many manufacturing job losses as in higher income regions, according to Oxford Economics.
The explanation is simple: people living in lower-income regions usually have a lower skill set, leaving them more vulnerable to automation as their tasks are, on average, relatively easier to automate. At the same time, the authors also say in these regions workers are, on average, less productive. So the truth is manufacturers face a big opportunity for efficiency savings and productivity gains. And as many industrial sites are outside the main urban areas, the people living close to them, where jobs are usually more precarious and with lower salaries, will be the ones affected the most as these will be the first sites to be automated.
Automation Is Taking Down Jobs – Now What?
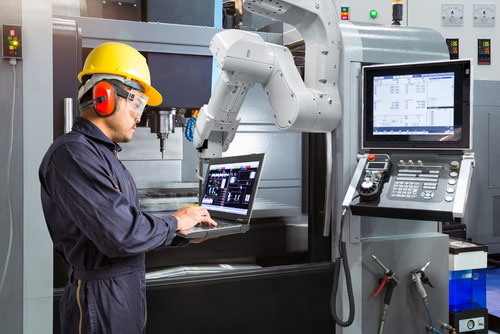
Now, we fight back robots. No, seriously, that’s probably not the best approach and we’ll reach their benefits just now. For now we need to anticipate these employment changes and proactively starting adapting the workforce to them. For instance, the fact that old jobs cease to exist doesn’t mean there won’t be new jobs coming up. There will. Because someone will need to code, develop, design, improve robots and automation overall, so we’ll likely need a more tech specialized workforce. And as Yuval Hariri states, philosophers will be needed as well – for instance, to help autonomous driving car manufacturers program their software to decide whether to run over a 10-year-old girl suddenly crossing the street or to crash the car, with children onboard, on the other side of the road.
Anyways, while robotics will create new employment opportunities across some segments of the economy, Orford Economics’ analysts say it’s unlikely they’ll equal the number of jobs displaced by automation. And this increased industrial automation will tendentiously intensify today’s regional inequalities. In fact, the study developed a vulnerability showing which showed the regions economically dependant on less productive manufacturing industries that are not currently automated – have a high risk of “meeting” robots soon. This vulnerability index shows economic performance, at a regional level, is inversely correlated with robot vulnerability – which leaves the regions that have performed the worst in recent years more exposed to automation in the future, and vice-versa.
At the same time, the major urban areas are safe for now as they rely on diversified economies less dependent of manufacturing jobs and the ability to pay these higher labor costs mean manufacturers are already highly productive and therefore tend to employ workers with a wider skill set. Moreover, rural areas have hidden vulnerabilities as in these regions people get a lower income, are more isolated, and have often been abandoned as people are increasingly moving to urban areas.
What’s also worrying is that workers displaced from manufacturing typically turn to the service sector, specifically to either the area of transports, construction and maintenance or office/ administration work. These are, according to the researchers, the 3 occupational categories most vulnerable to robotic developments and automation – and, therefore, something that deserves proper attention and planning.
The U.S. In Depth – How Vulnerable Is The U.S To Automation
According to Oxford Economics, Oregon is the most vulnerable state in the U.S., as the pace at which robots are being installed is accelerating. Despite the fact Oregon has been succeeding in producing high-tech goods and components, it still depends highly on manufacturing, especially around Portland. “The state’s exposure to globally competitive sectors means its workers are vulnerable to rapid technological progress”, the authors say.
Texas and Louisiana are two relatively vulnerable states in the South. As is Indiana in the mid-west. It is running on heavy industries such as steel-making, which creates some vulnerability. However, it is focusing on growing higher-value and knowledge-based industries, which will likely slow down the automation transition.
Less vulnerable are the New England states and the ones highly relying on tourism such as Hawaii, Nevada or Florida. The same happens with New York, which, despite also being a manufacturing base has a stronger focus on financial and business services.
How Will Automation Affect The Gender Agenda? Will Women Be Less Affected?
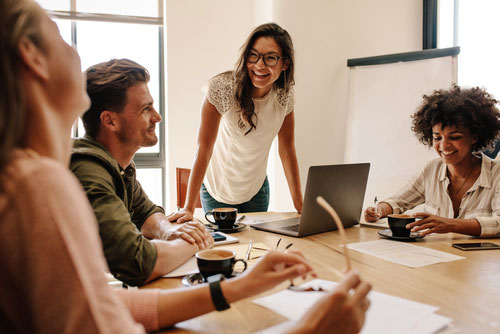
(Until now we’ve been relying mostly on data from Oxford Economics, which uses data from physical robots and tends to leave automation associated with bots or RPA aside. This chapter uses broader data from Mckinsey.)
So you might think “manufacturing, in general, employs more men, therefore, they’ll be in more need for a job than men”. Nope, not really. I mean, yes, craftwork and machine operations might account for 40% of men’s job losses (between 60-275 million jobs). But clerical support jobs (more administrative), as well as service-oriented jobs, might account for 52% of women’s job losses too (meaning 40 million to 160 million jobs). According to a Mckinsey study that highlights the data we just discussed, the sectors where both genders will have their chance of recovering are in manufacturing for men (if they’re able to keep up with technologies and learn to take the best out of machines) and the healthcare sector.
Mckinsey’s report suggests that in order to prevent these unbalances, it should be guaranteed that women keep (getting) a relevant role in the global workforce market. Futhermore, to promote a (as far as possible) smoothly transition, 3 main aspects should be considered. The first is about betting in training programs and platforms that enable women to develop the tech skills they’ll need. This includes both women working in subsistence agriculture with little education but also women in today’s “formal” job market who’ll need to refresh their skills and get more tech-savvy. And as they might be, generally speaking, more inclined to jobs more easily automated, they need to learn and build a new skill set alongside automated systems.
At the same time, the demand for higher-wage labor is likely to grow (also in emerging economies) and there are more women working in lower-paid occupations than men. Therefore, it’s important that women are encouraged to improve on their skills set (with tech skills included) so that it gets easier for them to grab job market opportunities and get into higher-paying jobs. Important too would be to prioritize childcare provision so that moms could have more time away from unpaid care work (still mostly performed by women) and use it instead to look for better job opportunities, develop a larger professional network or to attend trainings to learn new skills.
Automation And Robots Bring Along Many Benefits Too
Yes, robots and automation are synonyms with change. And humans seem to have a hard time embracing change. However, changes aren’t necessarily (or totally) bad, and there’s definitely another side of the coin. For instance, a 1% increase in the stock of robots per worker in the manufacturing sector can increase workers performance outputs by 0,1%. This means that by having automated jobs in this sector, robots can free up many people and allow them to give a more productive contribution elsewhere. And at the same time, a scenario of a large adoption of robots seems to able to boost global GDP by 5,3% – which would mean an extra $4.9 trillion to the global economy in 2030.
But there’s more. Way more. There’s more than we often think about happening today, and even more likely to happen tomorrow. For instance, nearly three-quarters of people work in the growing service sector. Developments in AI, machine learning and computing power will bring along changes. However, these changes will take quite some time as many jobs require unique human qualities such as social intelligence, imagination or empathy, which aren’t yet ready to get an algorithmic shape.
In the medical area, for instance, we can expect robots to have a growing presence in hospitals, clinics or assisted living homes as life-expectancy extends and the population gets older. And while robots transport blood samples to the lab or help cleaning, there will still be humans around – except they’ll have more time to listen and put empathy or compassion into use. Robot-assisted surgeries that allow doctors to operate more accurately are other increasingly common practices. New kinds of robots have already been built to lay bricks and install sheetrock and others to come will impose new changes. But again, maybe change isn’t entirely bad. I mean, it’s not like the overall population today is indeed very happy every when going to work on Mondays, right? Why not see these changes from a positive perspective too – as an opportunity to change the way work is currently organized?
- Related:
“Robots Are Coming, Fasten Your Seatbelts” (And The Car Automatically Does It Due To Voice Response)
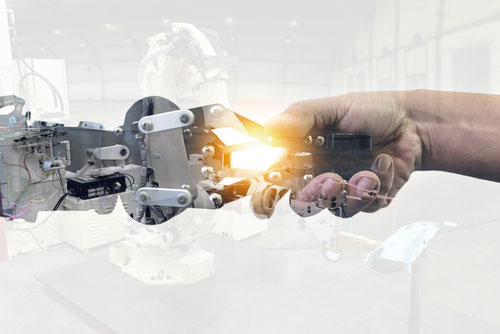
Mckinsey says 60% of occupations have at least 30 percent of constituent work activities that could be automated. And following their projections, by 2030, 75 million to 375 million workers (3 to 14 percent of the global workforce) will need to switch occupational categories. So the labor market will indeed be reshaped as automation and robots are both destroying old jobs and creating new ones. And these changes will bring both winners and losers, as millions of workers will see their old jobs be performed by new technologies, which is starting today with manufacturing jobs, especially in lower-income regions. This workforce will need to learn a new skills to be able to create robots and automate them. And at the same time, otherws able to live out their creativity or their social or emotional skills will be increasingly valued.
Robots bring along the chance of improving business productivity and, therefore, contributing to economic growth – which can something good if one believes growth is indeed what’s needed. Robots will keep revolutionizing the way societies live and are organized. And as we progress, they’ll likely challenge some of our deeper beliefs regarding decision-making processes (as AI starts approving bank loans) or emotions and consciousness (as nano-sensors enter or blood system and warn us of imminent heart strokes).
Decision-makers at all levels, need to balance all things involved in this automation equation. How to balance the potential gains of long-term robotization growth and its benefits with the short-term consequences of social dislocation, depression and insecurity, new (social?) systems to train unemployed people and empower them with a new techy skill set? Will people start working fewer hours, as Rutger Bergman, the Dutch historian supporting the universal basic income, suggests? Nothing is likely to remain untouched and everyone, from policy-makers to tech companies with CSR strategies, (social) entrepreneurs and professionals in the education field, they’ll all have a very important role to play.
- Related:
Image credits to the assembly on Shutterstock, laptop on Shutterstock, manager on Shutterstock, robotics on Shutterstock, engineer on Shutterstock, executive on Shutterstock and disruption on Shutterstock